The Science Behind Porosity: A Comprehensive Guide for Welders and Fabricators
Comprehending the detailed devices behind porosity in welding is vital for welders and producers striving for remarkable workmanship. From the structure of the base materials to the details of the welding process itself, a plethora of variables conspire to either intensify or minimize the presence of porosity.
Understanding Porosity in Welding
FIRST SENTENCE:
Exam of porosity in welding discloses critical insights into the integrity and high quality of the weld joint. Porosity, characterized by the presence of cavities or voids within the weld metal, is an usual problem in welding procedures. These voids, if not properly addressed, can endanger the structural integrity and mechanical buildings of the weld, leading to prospective failings in the ended up product.
To detect and evaluate porosity, non-destructive testing approaches such as ultrasonic testing or X-ray evaluation are typically employed. These strategies permit the recognition of internal issues without compromising the honesty of the weld. By examining the dimension, shape, and distribution of porosity within a weld, welders can make enlightened decisions to improve their welding procedures and achieve sounder weld joints.
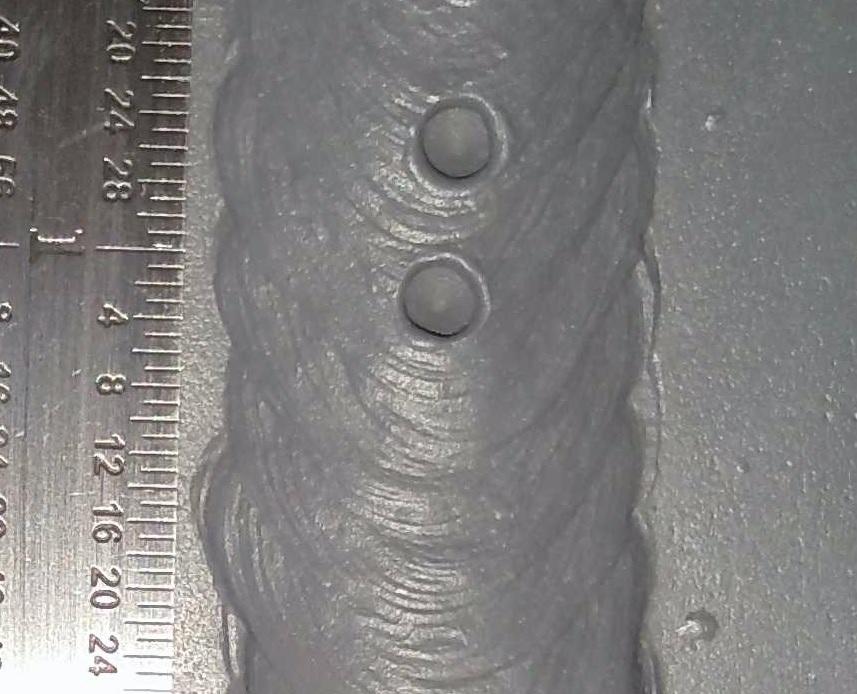
Elements Influencing Porosity Formation
The incident of porosity in welding is affected by a myriad of variables, varying from gas shielding effectiveness to the complexities of welding criterion settings. Welding specifications, including voltage, current, take a trip rate, and electrode kind, additionally influence porosity development. The welding technique used, such as gas steel arc welding (GMAW) or secured steel arc welding (SMAW), can influence porosity formation due to variants in warm circulation and gas insurance coverage - What is Porosity.
Impacts of Porosity on Weld Top Quality
The presence of porosity additionally compromises the weld's resistance to corrosion, as the trapped air or gases within the voids can respond with the surrounding environment, leading to degradation over time. Furthermore, porosity can impede the weld's ability to hold up against pressure or influence, further endangering the general top quality and integrity of the bonded structure. In critical applications such as aerospace, vehicle, or architectural constructions, where security and toughness are paramount, the detrimental results of porosity on weld high quality can have extreme repercussions, stressing the value of reducing porosity via proper welding strategies and treatments.
Methods to Reduce Porosity
To boost the quality of bonded joints and guarantee structural integrity, welders and fabricators employ particular techniques targeted at reducing the development of spaces and tooth cavities within the material during the welding process. One effective technique to lessen porosity see this is to make sure appropriate product preparation. This includes thorough cleaning of the base steel to get rid of any impurities such as oil, grease, or dampness that could add to porosity development. Furthermore, making use of the proper welding specifications, such as the appropriate voltage, present, and travel rate, is vital in protecting against porosity. Preserving a consistent arc size and angle during welding also helps in reducing the likelihood of porosity.

Utilizing the appropriate welding method, such as back-stepping or utilizing a weaving activity, can likewise aid distribute warmth uniformly and lower the opportunities of porosity formation. By carrying out these methods, welders can effectively lessen porosity and generate high-quality welded joints.

Advanced Solutions for Porosity Control
Implementing innovative innovations and innovative methods plays a crucial role in attaining exceptional control over porosity in welding procedures. In addition, employing innovative welding techniques such as pulsed MIG welding or modified ambience welding can also aid reduce porosity issues.
Another innovative service entails making use of innovative welding tools. Making use of devices with integrated features like waveform control and innovative power sources can boost weld quality and lower porosity threats. Moreover, the execution of automated welding systems with accurate control over criteria can dramatically minimize porosity flaws.
Furthermore, you could check here including sophisticated surveillance and inspection innovations such as real-time X-ray imaging or automated ultrasonic testing can help in finding porosity early in the welding procedure, enabling prompt restorative activities. On the whole, incorporating these innovative options can considerably boost porosity control and improve the overall high quality of welded parts.
Conclusion
In verdict, understanding the scientific research behind porosity in welding is vital for welders and producers to produce high-quality welds - What is Porosity. Advanced options for porosity control can even more improve the welding hop over to here procedure and guarantee a solid and dependable weld.